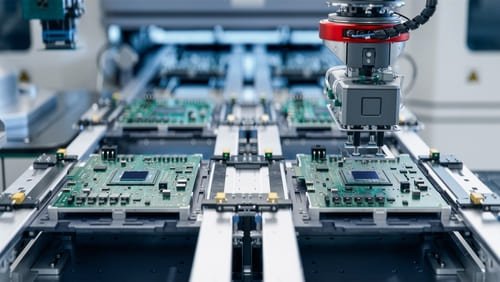
PCB Assembly
No matter your industry, you deserve a seamless process and reliable results. Whether you need prototypes or full-scale production, Magellan Circuits is here to deliver PCB assemblies tailored to your exact needs—designed to perform flawlessly and exceed your expectations.
Professional PCB Assembly Manufacturer
When it comes to PCB assembly, Magellan Circuits stands out as a trusted partner for businesses that demand precision, reliability, and efficiency. From prototypes to high-volume production runs, with over 20 years of expertise, we provide tailored assembly solutions that align with your project’s unique needs. Our state-of-the-art facility in Shanghai is equipped to handle the most complex assembly requirements, ensuring your boards are delivered on time and to the highest standards.
Why Choose Magellan Circuits for PCBA?
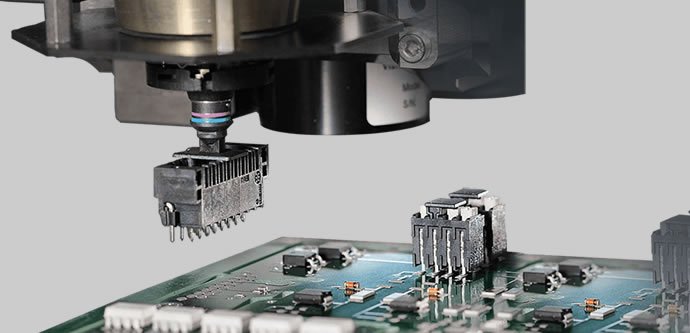
Seamless Integration
Magellan Circuits goes beyond standard assembly methods to ensure your PCBs are optimized for performance and manufacturability:
- High-Density Interconnect (HDI) Integration: Perfect for compact, high-performance designs, enabling efficient signal routing and enhanced reliability.
- Advanced Soldering Techniques: Precision-driven methods like vapor phase and selective soldering ensure consistent quality, even in complex assemblies.
- Hybrid Assembly Solutions: Expertise in integrating rigid, flex, and embedded components for versatile applications.
- Design Optimization Support: Collaborate with our engineers to fine-tune designs, reduce iterations, and lower costs without compromising functionality.
Rigorous Testing
Your PCBs undergo comprehensive testing using cutting-edge techniques to guarantee quality and reliability:
- In-Circuit Testing (ICT): Detects manufacturing defects, including shorts, opens, and incorrect component placements, ensuring assembly accuracy.
- Functional Circuit Testing (FCT): Simulates real-world conditions to validate the performance of assembled PCBs and ensure they meet design specifications.
- X-Ray Inspection: Provides detailed analysis of solder joints and internal layers, particularly for hidden components like BGAs, ensuring flawless assembly integrity.
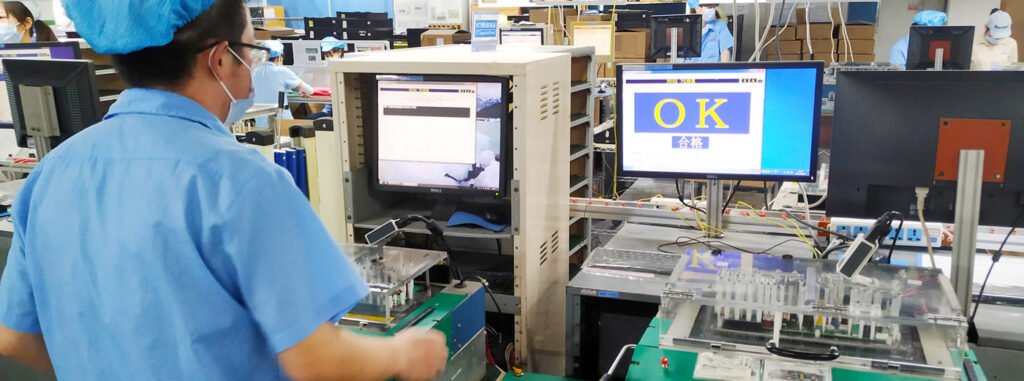
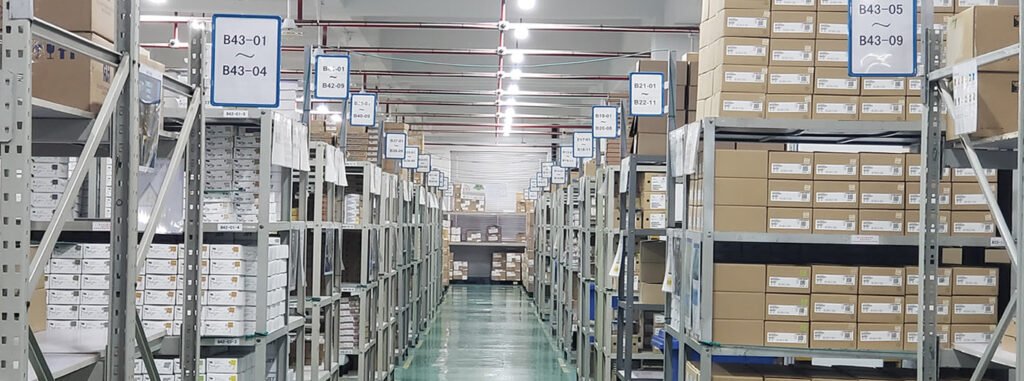
Proactive Sourcing and Supply Chain Management
Magellan Circuits ensures that your projects stay on schedule with robust sourcing capabilities:
- Global Supplier Network: We secure high-quality components from trusted suppliers to mitigate delays caused by shortages.
- Efficient Inventory Management: Strategically managed component storage reduces lead times and ensures smooth project execution.
- Alternative Sourcing Solutions: Proactively identifies substitute components to keep your production on track.
Global Delivery
With a well-established logistics network, Magellan Circuits delivers PCBs efficiently and reliably to clients worldwide:
- Timely Deliveries: On-time shipments to regions including North America, Europe, Asia, and more.
- Streamlined Customs Handling: Expertise in navigating international shipping requirements ensures hassle-free delivery.
- Responsive Support: Dedicated teams to address inquiries and resolve challenges quickly, no matter your location.
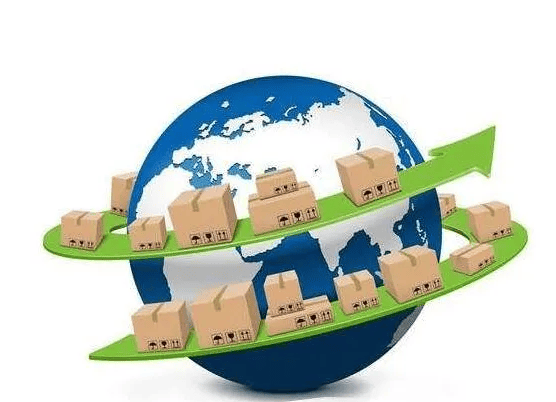
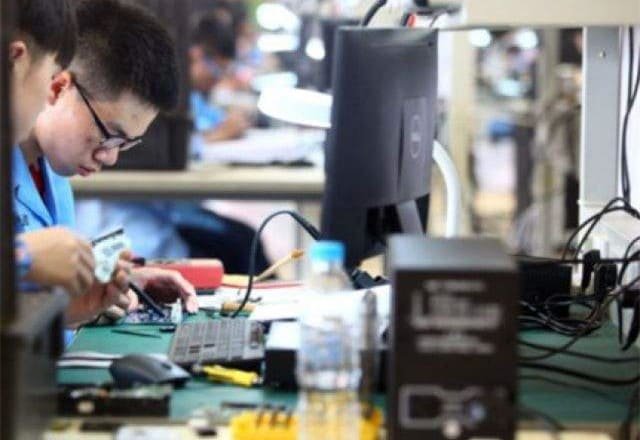
Unmatched Expertise
At Magellan Circuits, our team’s experience and certifications set us apart:
- Over 20 years of industry expertise, serving diverse industries such as AI hardware, automotive, medical devices, aerospace, and telecommunications.
- Certified to ISO 9001, ISO 14001, ISO 45001, OHSAS 18001, RoHS, REACH, UL and IATF 16949 standards, ensuring compliance with global quality benchmarks.
- Proven track record of delivering exceptional results for Fortune 500 companies and startups alike.
Our PCB Assembly Solutions for Every Industry
Magellan Circuits provides assembly solutions tailored to your unique industry needs:
- AI Hardware Products: Your designs demand high-speed signal integrity, power optimization, and thermal management. Our assemblies handle intensive workloads for cutting-edge AI and machine learning systems.
- Automotive: Rely on durable, safety-compliant assemblies that meet the rigorous standards of automotive applications.
- Medical Devices: Trust in precision-engineered boards for life-critical applications, ensuring reliability under strict performance demands.
- Telecommunications: Seamlessly connect your networks with high-frequency assemblies designed for efficient signal processing.
- Aerospace: Lightweight, robust designs built to endure extreme environments and high performance demands.
- Consumer Electronics and Robotics: Flexible, innovative solutions that match your dynamic product requirements.
PCB Assembly Capability
When precision and reliability matter, our PCB assembly capabilities provide the flexibility and expertise you need. Whether your project requires Surface Mount Technology (SMT) or Through-Hole Technology (THT), we ensure seamless assembly tailored to your design specifications. For compact and high-performance boards, our HDI assembly solutions offer optimized layouts with exceptional reliability. To ensure quality where it counts, we offer testing options such as In-Circuit Testing (ICT), Functional Circuit Testing (FCT), and X-Ray Inspection, providing the assurance you need for critical applications.
SMT Capability
Category | Capability |
---|---|
Printing | |
Max Processable PCB Size | 510 mm *510 mm |
Maximum Board Weight | 5 kg |
Printing Accuracy | ±18 μm(6σ) |
System Calibration Repeatability | ±12.5 μm(6σ) |
Squeegee Pressure Detection | Pressure Closed-Loop Control System |
Surface Mounting | |
Min Detectable Solder Ball Pitch | 100 μm |
X-Y Axis Accuracy | 10 μm |
False Detection Rate | ≤0.1% |
Min Component Size | 0.3 mm*0.15 mm (01005) |
Max Component Size | 120 mm*90 mm |
Max Component Height | 30 mm |
Max Component Weight | 30 g |
BGA/CSP Min Ball Pitch | 0.30 mm |
BGA/CSP Min Ball Diameter | 0.25 mm |
Placement Accuracy | ±30 μm (3σ) |
Min Processable PCB Size | 50 mm*50 mm |
Max Processable PCB Size | 750 mm*550 mm |
Min PCB Thickness | 0.3 mm |
Max PCB Thickness | 8 mm |
Max Board Weight | 3 kg |
Max Number of Material Types per Line | 500 |
Reflow | |
Temperature Accuracy | ±1 ℃ |
Soldering Protection | Nitrogen Protection (Residual Oxygen < 3000 ppm) |
Nitrogen Control | Nitrogen Closed-Loop Automatic Control System, ±200 ppm |
Through-Hole Assembly Capability
Category | Capability |
---|---|
Pre-processing | Automatic Component Forming |
Insertion | Fully Automatic Insertion |
Wave Soldering | |
Wave Type | Standard Wave |
Conveyor Rail Angle | 4°–7° |
Standard Wave Soldering Temperature Accuracy | ±3 ℃ |
Selective Wave Soldering Precision | ±0.06 mm |
Press-fit Technology | |
Max PCB Size | 800 mm*600 mm |
Press Height Accuracy | ±0.02 mm |
Pressure Range | 0–50 KN |
Pressure Accuracy | ±2% of the standard value |
Dwell Time | 0—9.999 s |
Conformal Coating Capability
Category | Capability |
---|---|
Max Board Size | 450 mm*450 mm*6 mm |
Max Single Board Weight | 5 kg |
Min Nozzle Diameter | 2 mm |
Other Features | Programmable spray pressure control |
Washing Capability
Category | Capability |
---|---|
Max Assembly Width | 457.2 mm |
Max Assembly Height | 102 mm |
Equipment Functions | Single/Double Hurricane Jets, S-Type Nozzles, Air Knife |
Testing Capability
Category | Capability |
---|---|
AOI | |
Min Detectable Component | 01005 |
Defect Detection |
Wrong Part, Missing Part, Reverse Polarity, Placement Offset, Tombstoning, Side Standing, Open Solder Joint, Solder Bridging, Flipped Component |
Lifted Lead Detection | Bent Lead |
ICT Testing | |
Test Level | Component-level, hardware connection testing |
Number of Test Points | >2500 points |
Test Content |
Contact test, open/short circuit test, resistance/capacitance test, second/third-level FET test, unpowered mixed test, boundary scan chain test, powered mixed-mode test |
FCT Testing | |
Test Level | System-level testing of circuit boards, testing system functional status |
Reliability Tests | Aging, drop, vibration, wear, key lifespan tests |
2D X-Ray Inspection | |
Magnification | Geometric: 2000×; System: 12000× |
Resolution | 1 μm |
Rotation & Tilt Angle | Any ±45°, + 360° rotation |
AXI (Automated X-ray Inspection) | |
Min Detectable Component | 01005 |
Min Detectable Lead Pitch | 0.4mm(QFP) |
Min Detectable Solder Thickness | 0.0127 mm |
Ready to Collaborate
with Magellan Circuits?
What is PCB Assembly?
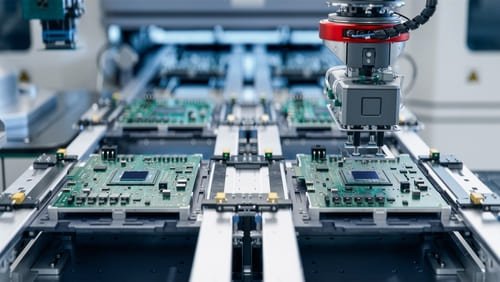
PCB assembly (PCBA) is the process of mounting and soldering electronic components onto a bare printed circuit board (PCB) to create a fully functional electronic circuit. It involves placing components, such as resistors, capacitors, and integrated circuits, onto the PCB using methods like Surface Mount Technology (SMT) for compact and automated assembly or Through-Hole Technology (THT) for more durable and mechanically strong connections.
SMT vs. THT: Which One is Right for Your Project?
Surface Mount Technology (SMT) and Through-Hole Technology (THT) are two primary methods used in PCB assembly, each suited to different project requirements:
SMT (Surface Mount Technology): Components are mounted directly onto the PCB surface without the need for drilled holes. SMT is ideal for:
- Compact and lightweight designs.
- High-density boards with complex circuitry.
- Automated, high-speed assembly processes.
THT (Through-Hole Technology): Components have leads that are inserted into drilled holes and soldered on the opposite side of the board. THT is best for:
- Boards requiring strong mechanical connections, such as those used in automotive or industrial applications.
- Projects where durability and reliability are priorities.
The choice between SMT and THT depends on your project’s specific needs. In many cases, a combination of both technologies is used to balance compact design with mechanical stability, particularly for high-performance or multi-functional boards.
Key Soldering Methods in PCB Assembly
Soldering is a fundamental step in PCB assembly, responsible for attaching electronic components securely to the board and ensuring reliable electrical connections. The three primary soldering methods used in the industry are Reflow Soldering, Wave Soldering, and Selective Soldering.
Reflow Soldering is the most common technique for surface-mounted components. In this method, solder paste is applied to the PCB pads, components are placed onto the paste, and the board is passed through a controlled reflow oven. The oven heats the board to melt the solder paste, forming solid connections between the components and the PCB.
Wave Soldering is typically used for through-hole components. The PCB is exposed to a continuous wave of molten solder that flows through the drilled holes, bonding the leads to the board.
Selective Soldering is a targeted approach for soldering specific areas of the PCB. It is often used when a board combines surface-mounted and through-hole components or has heat-sensitive areas. Techniques like mini-wave soldering and laser soldering ensure solder is applied only where needed, minimizing thermal stress and protecting nearby components.
Each of these soldering methods plays a critical role in ensuring the mechanical strength and electrical integrity of PCB assemblies, supporting a wide range of applications across industries.
What Is the Difference Between Leaded and Lead-Free Solder in PCB Assembly?
Leaded and lead-free solder are two types of materials used in PCB assembly, each with distinct characteristics, advantages, and applications.
Leaded Solder contains a combination of tin and lead, typically in a 63/37 ratio (63% tin, 37% lead). It has a lower melting point (around 183°C or 361°F), which reduces thermal stress on components and the PCB during soldering. Leaded solder is easier to work with due to its excellent wettability and smoother flow, making it ideal for applications where reliability and ease of manufacturing are priorities. However, due to environmental concerns and regulations such as RoHS (Restriction of Hazardous Substances), the use of leaded solder is restricted in many industries.
Lead-Free Solder, by contrast, replaces lead with other metals such as silver, copper, or bismuth. It has a higher melting point (typically around 217–227°C or 423–441°F), which requires higher processing temperatures during soldering. While this can increase thermal stress, lead-free solder is environmentally friendly and complies with global standards for hazardous material restrictions. It is commonly used in industries like consumer electronics, medical devices, and telecommunications, where RoHS compliance is mandatory.
The choice between leaded and lead-free solder depends on factors like regulatory requirements, thermal tolerance of components, and the end application. While leaded solder offers superior ease of use, lead-free solder is essential for eco-conscious and compliant manufacturing.
What Are the Common Defects in PCB Assembly?
During PCB assembly, certain defects can affect the performance and reliability of your electronic devices. Understanding these issues and how they are addressed ensures your project runs smoothly and avoids costly rework. Below are the most common assembly-related defects and how they are managed:
Solder Bridges
Solder bridges occur when excess solder forms unintended connections between adjacent pads or component leads, causing short circuits. This issue can arise during reflow soldering for SMT components or wave soldering for THT components.
- How It’s Prevented: Precision solder paste application, accurate wave soldering parameters, and thorough inspection help eliminate the risk of solder bridges.
Solder Balling
Small solder balls can form during reflow or wave soldering, leading to contamination or short circuits. This defect often results from excessive solder paste, poor reflow conditions, or inadequate cleaning of PCB surfaces.
- How It’s Prevented: Optimize solder paste volume, ensure consistent wave soldering profiles, and maintain clean PCBs before assembly.
Cold Solder Joints
Cold solder joints occur when solder doesn’t properly flow and adhere to the pad or component, creating weak or incomplete connections. This defect is common in reflow, wave, or selective soldering if temperatures are not adequately controlled.
- How It’s Prevented: Proper thermal profiling during soldering and monitoring of solder flow ensure strong and reliable joints.
Component Misalignment
Misaligned components may occur during automated placement in SMT processes or during handling in THT assembly, leading to poor connectivity or mechanical instability.
- How It’s Prevented: Regular calibration of pick-and-place equipment, use of fiducial markers for alignment, and post-placement inspections help ensure accurate positioning.
Tombstoning
This defect happens when one end of a small SMT component lifts off the PCB during soldering, breaking its connection. Uneven heating or unbalanced solder paste deposition typically causes this issue.
- How It’s Prevented: Use properly designed solder stencils, apply even solder paste, and ensure consistent heating during the reflow process.
By working with an assembly partner that implements these preventive measures, you can ensure your PCBs are built to perform reliably and meet the high standards of industries like automotive, telecommunications, and medical devices.
What Factors Impact the Quality of PCBA?
The quality of PCB assembly directly influences the reliability and performance of the final product. Several key factors play a critical role in ensuring a high-quality assembly:
Component Quality
The reliability of the assembled PCB starts with the quality of its components. Using authentic, defect-free components ensures that the board performs as intended and avoids issues such as premature failure or electrical instability.
Soldering Processes
The soldering method—whether reflow, wave, or selective soldering—must be executed with precision. Factors like solder paste quality, proper temperature control, and accurate application determine the strength and conductivity of solder joints.
PCB Design and Layout
A well-designed PCB simplifies assembly and minimizes the risk of defects. Proper component placement, trace routing, and adherence to Design for Assembly (DFA) principles are crucial for smooth manufacturing and optimal board performance.
Assembly Equipment Calibration
Modern PCB assembly relies on automated processes like pick-and-place machines and reflow ovens. Regular calibration and maintenance of this equipment ensure consistent accuracy and prevent defects such as misaligned components or incomplete soldering.
Cleanliness of Materials
Contaminants like dust, oil, or residue on the PCB surface or components can interfere with soldering and lead to defects like weak joints or solder balling. Clean materials and controlled environments are essential for high-quality assembly.
Testing and Inspection
Comprehensive testing, such as In-Circuit Testing (ICT), Functional Circuit Testing (FCT), and Automated Optical Inspection (AOI), plays a vital role in identifying and correcting assembly issues before deployment. This ensures reliability and compliance with performance standards.
Operator Expertise
Even with advanced automation, skilled operators are essential for quality control and troubleshooting. Experienced personnel ensure smooth processes, from solder paste application to final inspection.
By ensuring these factors are addressed, you can rely on your assembly partner to deliver high-quality PCB assemblies that reduce rework, enhance product reliability, and support the success of your projects.
How Does Testing Ensure PCBA Reliability?
Testing is a critical step in PCB assembly, ensuring that the assembled boards meet performance standards and are free from defects before deployment. Advanced testing methods, often combined with custom fixtures, validate both functionality and reliability.
In-Circuit Testing (ICT) uses custom-designed test fixtures to evaluate the electrical performance of individual components and connections on the PCB. By applying probes to specific test points, ICT identifies shorts, opens, and incorrect component values, ensuring the board matches its design specifications. This method is highly effective for detecting assembly issues early in the process.
Functional Circuit Testing (FCT) involves simulating real-world operating conditions to verify the overall functionality of the PCB. FCT often relies on fixtures tailored to the board’s design to test specific inputs, outputs, and functionality. This ensures that the PCB operates as intended in its application, catching any latent defects before deployment.
X-Ray Inspection provides a non-destructive way to examine solder joints and internal connections, especially in assemblies with hidden components like Ball Grid Arrays (BGAs). This method detects voids, misalignments, and soldering defects that may not be visible through optical inspection.
By combining advanced testing methods with precise fixtures designed for your PCB, assembly processes can identify and resolve potential issues effectively. This ensures that every PCB delivered is reliable, functional, and ready to meet the demands of its intended application.
FAQ
The files required for PCB assembly depend on whether you’re starting from scratch or providing a pre-fabricated PCB. Below are the requirements for each scenario:
Scenario 1: Starting from Scratch (Including PCB Manufacturing)
If you need both PCB manufacturing and assembly, the following files are required:
- Gerber Files: Detailed PCB layout files, including copper layers, solder mask, silkscreen(optional), and drill data, required for manufacturing the PCB.
- Bill of Materials (BOM): A professional BOM must include the following:
- Company Part Number: A unique identifier used internally by your company for tracking components.
- Component Part Numbers: Manufacturer’s or distributor’s part numbers to ensure accurate sourcing.
- Quantities: The number of each component required for a single board.
- Value: The electrical specification of the component (e.g., resistor values, capacitor ratings).
- Designators: Labels like R1, C2, or U3 that map components to their positions on the PCB.
- Alternate Part Numbers: Backup components for sourcing flexibility in case of shortages.
- Footprint: The package name of the component (e.g., 0603, SOT-23, QFN), which ensures compatibility with the PCB layout and assembly process.
For multi-SKU products, create a Master BOM that lists all components for every SKU. Include a separate column or sheet indicating which components are used for each SKU. This approach avoids confusion and ensures that the correct components are assembled for each variation.In different companies, there are other varying approaches.
- Pick-and-Place File (Centroid File): Provides X-Y coordinates, rotation, and board side (top or bottom) for all components.
- Stencil Data (Gerber for Solder Paste Layer): Specifies the stencil design for solder paste application during SMT assembly.
- Assembly Drawings: Visual guides showing component placement and orientation. For multi-SKU products, include separate assembly drawings for each SKU, clearly highlighting variations in component placement or assembly instructions.
- Testing Requirements: Provide the following testing files for functional or in-circuit testing:
- Test Specification Document: A detailed description of the tests to be performed, including the methodology.
- Test Point Layouts: Gerber files indicating the locations and labels of test points.
- Expected Results: Parameters (e.g., voltage levels, current values) for validating the board’s functionality.
Scenario 2: Providing a Fabricated PCB (Surface Mounting Only)
If you already have a fabricated PCB and only need components mounted, the following files are required:
- Bill of Materials (BOM): Include the same elements as above but tailor it for multi-SKU scenarios. A Master BOM should cover all components across SKUs, with a clear indication of which components apply to each SKU. This can be achieved by:
- Adding a column to denote SKU applicability for each component (e.g., “SKU A,” “SKU B”).
- Creating a separate BOM for each SKU if variations are extensive, ensuring clarity and avoiding errors.
- Pick-and-Place File (Centroid File): Includes X-Y coordinates, rotation, and board side (top or bottom) for each component.
- Stencil Data (Gerber for Solder Paste Layer): Ensures precise solder paste application for SMT assembly.
- Assembly Drawings: Include tailored drawings for each SKU, clearly indicating component variations. Ensure that assembly differences are visually distinct to minimize errors during the process.
- Testing Requirements: Provide the following testing files for functional or in-circuit testing:
- Test Specification Document: A detailed description of the tests to be performed, including the methodology.
- Test Point Layouts: Gerber files indicating the locations and labels of test points.
- Expected Results: Parameters (e.g., voltage levels, current values) for validating the board’s functionality.
At Magellan Circuits, we employ proactive strategies to address component shortages and sourcing delays, ensuring your projects stay on track.
We maintain a robust supplier network by collaborating with trusted global suppliers. This enables us to source components from multiple channels and secure alternatives quickly if specific parts are unavailable.
For long lead-time components, such as certain FPGAs with procurement cycles extending up to 52 weeks, we recommend and facilitate advanced purchasing. By procuring critical components ahead of production schedules, we ensure their availability when needed, minimizing potential delays.
Our inventory management system helps us monitor stock levels and anticipate demand. This allows us to act proactively in securing parts before shortages occur. For critical or high-demand components, we also maintain buffer stock to ensure continuity during supply chain disruptions.
To reduce risks, we encourage customers to include alternate part numbers in their Bill of Materials (BOM). These pre-approved substitutes provide flexibility, allowing assembly to continue even if primary components are unavailable.
In urgent cases, we rely on expedited shipping to fast-track delivery of critical components. Air freight and priority courier services significantly shorten transit times, ensuring your project stays on schedule.
For hard-to-find components, we leverage premium procurement services, which provide access to exclusive inventories and specialized sourcing networks. This ensures that critical parts are secured even in constrained markets, though premium pricing may apply.
By sourcing exclusively from authorized distributors, we ensure the authenticity and traceability of all components, reducing the risks of counterfeit parts and unexpected delays caused by quality issues.
Finally, we maintain close collaboration with customers throughout the process. By identifying high-risk components early and tailoring procurement strategies to specific needs, we minimize disruptions and keep your projects on track.
Magellan Circuits offers a comprehensive suite of in-house testing capabilities, ensuring your PCB assemblies meet stringent quality and reliability standards. Our state-of-the-art infrastructure and tailored processes deliver accurate results for every project.
In-Circuit Testing (ICT)
Our ICT systems are equipped to handle over 2,500 test points, making them ideal for large and complex PCBs.
- Detects shorts, opens, incorrect component values, and solder joint defects.
- Custom-built test fixtures ensure precise and reliable testing for any PCB design.
- Efficient for both high-volume production and prototypes, catching assembly defects early to minimize rework.
Functional Circuit Testing (FCT)
FCT validates the performance of fully assembled PCBs by simulating real-world operating conditions.
- Custom hardware and software setups ensure the PCB functions as intended in its final application.
- Identifies hidden defects such as communication faults between components and system-level malfunctions.
- Flexible for various designs, from simple boards to intricate multilayer assemblies.
Automated Optical Inspection (AOI)
Our high-speed AOI systems deliver fast and precise inspection of surface-level defects.
- Detects soldering issues, component misalignments, and polarity mismatches with high accuracy.
- Suitable for PCBs of all sizes and layouts, making it ideal for both low- and high-volume production.
X-Ray Inspection
Advanced X-ray systems allow us to inspect concealed solder joints and internal structures.
- Ideal for Ball Grid Arrays (BGAs) and other hidden components.
- Identifies voids, cracks, misalignments, and solder defects not visible through optical inspection.
- A non-destructive testing method that ensures quality without damaging the assembly.
Flying Probe Testing
For prototypes or low-to-medium production volumes, flying probe testing offers flexibility without requiring custom fixtures.
- Tests continuity, resistance, and capacitance with high precision.
- Cost-effective for smaller runs or designs still in development.
Environmental and Stress Testing
We subject PCB assemblies to rigorous environmental and stress testing to ensure reliability and durability in real-world conditions. These tests include:
- Aging Tests: Simulate extended operational use to detect early-life failures.
- Drop Tests: Assess mechanical integrity and resilience under impact forces.
- Vibration Testing: Ensure reliability in dynamic environments such as automotive or aerospace applications.
- Wear Tests: Validate the durability of components under repeated friction or mechanical stress.
- Key Lifespan Tests: Specifically assess the durability and responsiveness of mechanical buttons or keys, ensuring consistent functionality over thousands of cycles.
- Thermal Cycling: Evaluate solder joint and material performance under rapid temperature changes.
- Humidity Testing: Assess reliability in high-moisture environments, ensuring long-term stability.
By combining these environmental and stress tests, Magellan Circuits ensures your assemblies meet the demands of challenging operational conditions.
At Magellan Circuits, we understand that protecting your intellectual property (IP) is critical when working with custom PCB designs. We take comprehensive measures to safeguard your designs and ensure confidentiality at every stage of the manufacturing and assembly process.
Strict Non-Disclosure Agreements (NDAs)
Upon request, we sign legally binding NDAs to guarantee that your proprietary information will not be shared with third parties or used outside the scope of your project. This provides an additional layer of assurance for sensitive or high-stakes projects.
Controlled Access to Design Files
Access to your design files is restricted to authorized personnel only. Our internal systems are secured with role-based permissions, ensuring that only team members directly involved in your project can view or modify your data.
On-Site Manufacturing and Assembly
All manufacturing and assembly processes are conducted in-house at our secure facilities, reducing the risk of exposure to external parties. By minimizing the use of subcontractors, we maintain full control over your project’s confidentiality.
Employee Confidentiality Training
Our staff is regularly trained on the importance of IP protection and confidentiality. Strict policies and procedures are in place to prevent accidental breaches, reinforcing our commitment to safeguarding your designs.
Customizable IP Protection Measures
We understand that every customer’s needs are unique. For projects requiring additional security, we can implement customized IP protection measures, such as segregated workspaces, to ensure maximum confidentiality.
Yes, Magellan Circuits offers expedited services to meet the demands of urgent production runs. We understand that tight timelines are often critical, and we have dedicated processes in place to ensure fast and reliable delivery without compromising quality.
Prioritized Production Scheduling
For expedited orders, we adjust our production schedule to prioritize your project. This ensures that your PCBs are moved to the front of the production queue, significantly reducing lead times.
Streamlined Material Sourcing
We leverage our robust supplier network and premium procurement services to secure critical components quickly. For hard-to-find parts, we use specialized sourcing channels and expedited shipping options to prevent delays.
Flexible Manufacturing Capabilities
Our agile manufacturing processes are designed to accommodate rush orders, including:
- Faster turnaround times for PCB fabrication.
- Optimized assembly workflows to minimize downtime between stages.
Expedited Shipping Solutions
We collaborate with trusted logistics partners to ensure fast and secure delivery. Whether through express courier services or air freight, we select the most efficient shipping options to meet your deadlines.
Consultation for Feasibility
For especially urgent projects, we work closely with you to evaluate feasibility and establish realistic timelines. Our team provides recommendations on design adjustments, material substitutions, or other optimizations to accelerate the process further.
By combining these measures, Magellan Circuits ensures that your urgent production needs are met with speed, precision, and reliability.
Yes, Magellan Circuits can handle kitted or consigned assembly orders, offering flexible solutions to meet your specific requirements. Whether you prefer to supply all or some of the components for your PCB assembly, we adapt our processes to ensure seamless integration into your project.
Yes, Magellan Circuits offers both IC programming and conformal coating services as part of our comprehensive PCB assembly capabilities.
IC Programming
We provide IC programming services to ensure that integrated circuits are pre-programmed and ready for operation when installed on your PCB.
- Programming Flexibility: We support a wide range of ICs, including microcontrollers (MCUs), FPGAs, EEPROMs, and flash memory.
- Programming Methods: ICs can be programmed through on-board test points or dedicated sockets, depending on your design requirements.
- File Management: Simply supply us with your programming files, firmware, or configurations, and we’ll ensure precise programming with proper verification.
- Batch Programming: Whether you need programming for prototypes or large production runs, we scale our services to meet your needs.
Conformal Coating
We also provide conformal coating services to protect your PCB assemblies from environmental factors such as moisture, dust, and corrosion.
- Coating Types: We work with various conformal coating materials, including acrylic, silicone, urethane, and parylene, depending on your project’s specific needs.
- Application Methods: Our process includes spray coating, brush coating, or dip coating to ensure even and consistent protection.
- Selective Coating: Areas that require electrical contact, such as connectors, are carefully masked off to maintain functionality.
By offering IC programming and conformal coating, Magellan Circuits provides a one-stop solution for ensuring your PCBs are not only functional but also protected against external factors, saving you time and effort in post-assembly processes.
Yes, Magellan Circuits offers comprehensive turnkey solutions that cover the entire process—from PCB design to manufacturing and assembly. Our turnkey services are designed to streamline your project, reduce complexity, and ensure high-quality results.
Turnkey Design Services
Our design team works closely with you to transform your concept into a manufacturable PCB layout.
- Schematic Design: We translate your ideas into detailed circuit schematics.
- PCB Layout: Our experienced designers create efficient layouts that balance performance, cost, and space constraints.
- Signal Integrity (SI) and Power Integrity (PI): We ensure optimal performance for high-speed designs and power distribution networks, addressing critical issues such as crosstalk, noise, and voltage drops.
- Design for Manufacturability (DFM): Every design is optimized for smooth production, reducing the risk of delays or defects during manufacturing.
- Prototyping and Validation: We offer rapid prototyping to test and refine designs before full production.
Turnkey Manufacturing Services
From sourcing components to final assembly, we manage every step of the production process.
- Component Sourcing: We leverage our global supplier network to source high-quality components at competitive prices.
- PCB Fabrication: Our advanced manufacturing facilities handle PCBs of varying complexities, including multilayer and HDI designs.
- Assembly: We use state-of-the-art SMT and THT equipment for precise and reliable assembly.
- Testing and Quality Assurance: All products undergo rigorous testing, including AOI, ICT, FCT, and environmental stress screening, to ensure they meet your requirements.
Advantages of Our Turnkey Solutions
- Single Point of Contact: With all processes managed in-house, you save time and avoid the challenges of coordinating multiple vendors.
- Faster Time to Market: Streamlined processes and close collaboration ensure that your product moves from concept to production quickly and efficiently.
- Cost Savings: Consolidating design, manufacturing, and assembly under one provider reduces overhead costs and minimizes the risk of miscommunication.
- Scalability: Whether you need a small prototype run or high-volume production, our turnkey solutions scale to meet your needs.
By offering end-to-end turnkey solutions, Magellan Circuits enables you to focus on innovation and market strategies while we handle the technical complexities of design and production.