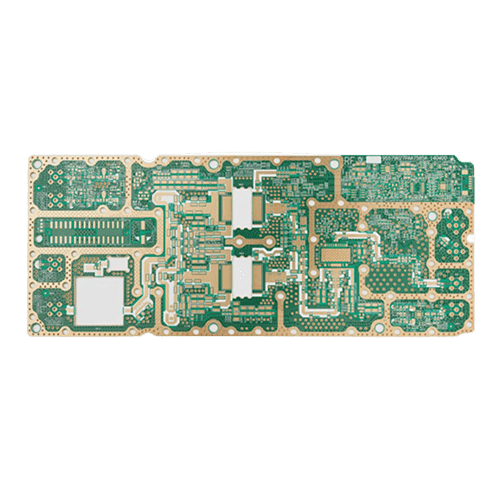
RF PCB
Magellan Circuits specializes in producing high-precision RF PCBs, ensuring superior signal integrity and precise impedance control for your advanced applications. Our state-of-the-art facilities and experienced team deliver reliable, efficient, and high-quality services to meet your specific needs.
Top Quality RF PCB Manufacturer
Magellan Circuits, located in Shanghai, is a leader in the production and development of high-precision RF printed circuit boards. We offer professional, reliable, efficient, and high-quality services to domestic and international high-tech enterprises and research institutions. Our advanced facilities and experienced team ensure rapid production of top-quality RF PCBs, widely used in various fields such as communication, aerospace, medical, automotive, and industrial control.
RF PCB Fabrication Capability
At Magellan Circuits, we bring advanced RF PCB fabrication capabilities to life, delivering solutions tailored for high-frequency applications. Our expertise ensures precise impedance control, low signal loss, and reliable performance for even the most demanding RF designs.
Board Parameters for RF PCB
Feature | Standard | Advanced |
---|---|---|
Material |
- Medium Loss: TUC TU862HF, EMC EM370D, ITEQ IT170GRA, Panasonic Megtron-2, etc. - Low Loss: Nelco N4000-13 (Series), Panasonic Megtron-4, S7038, S7439, TUC TU872SLK (Series), EMC EM-828, EMC EM-888, Nelco N4800-20 (Series), etc. |
- Very Low Loss: Panasonic Megtron-6, ITEQ IT150DA, Shengyi FL-700, Rogers RO4350B, Rogers RO3000 (Series), Taconic TLX (Series), Shengyi FL-700LD, etc. - Ultra-Low Loss and High Thermal Reliability: TUC TU993, Panasonic M6N, Panasonic M7N |
Layer Count | 1-26 | up to 40 |
Max Delivery Size | 609 x 508 mm | 1204 x 560 mm |
Min Board Thickness (Double-Sided) | 0.30 mm | 0.20 mm |
Min Board Thickness(4+ layers) | 0.60 mm | 0.45 mm |
Max Board Thickness | 4.0 mm | 10.0 mm |
Min Dielectric Thickness | 0.05 mm | 0.025 mm |
Copper-Filled Via Plating | No | No |
Copper Paste Plugged Via | Yes | Yes |
Via-in-Pad | Yes | Yes |
LDI | Yes | Yes |
Min Trace Width/Spacing (Inner Layer) | 0.05 mm | 0.05 mm |
Min Trace Width/Spacing (Outer Layer) | 0.05 mm | 0.05 mm |
Layer-to-Layer Alignment Tolerance | 0.05 mm | 0.025 mm |
Min Mechanical Drill Hole Size | 0.15 mm | 0.10 mm |
Min Laser Drill Hole Size | 0.075 mm | 0.05 mm |
PTH Aspect Ratio | 10:1 | 12:1 |
Finished Hole Tolerance (PTH) | ±0.076 mm | ±0.05 mm |
Finished Hole Tolerance(NPTH) | ±0.0375 mm | ±0.025 mm |
Max Outer Layer Copper Thickness | 6 oz | 120 oz |
Max Inner Layer Copper Thickness | 4 oz | 6 oz |
Impedance Control Tolerance | ±10% | ±5% |
Solder Mask Plugged Via IPC-4761 Type 6 | Yes | Yes |
Resin Plugged Via IPC-4761 Type 6 | Yes | Yes |
Resin Plugged Via IPC-4761 Type 7 | Yes | Yes |
Surface Finish Parameters for RF PCB
Feature | Standard | Advanced |
---|---|---|
Immersion Gold | Yes | Yes |
Gold Finger | Yes | Yes |
OSP | Yes | Yes |
Immersion Silver | Yes | Yes |
Leaded HASL | Yes | Yes |
Lead-Free HASL | Yes | Yes |
ENIG | Yes | Yes |
Immersion Tin | Yes | Yes |
Gold Finger + OSP | Yes | Yes |
Gold Finger + Lead-Free HASL | Yes | Yes |
OSP + Immersion Gold | Yes | Yes |
Immersion Silver + Gold Finger | Yes | Yes |
Immersion Tin + Gold Finger | Yes | Yes |
ENEPIG | Yes | Yes |
Ready to Collaborate
with Magellan Circuits?
What are RF PCBs?
RF PCBs, or Radio Frequency Printed Circuit Boards, are specialized types of printed circuit boards designed to operate at radio frequencies, typically in the range of 20 kHz to 300 GHz in RF engineering. These PCBs are crucial for the transmission and reception of radio signals and are used in various applications, including wireless communication, radar systems, and high-frequency signal processing.
Why Choose RF PCBs?
RF PCBs are designed to handle frequencies from 3 kHz to 300 GHz, ensuring minimal signal loss and clear transmission. This is particularly important for applications like wireless communication and radar systems.
With RF PCBs, you get precise impedance control, typically with a tolerance of ±10% to ±5%, to prevent signal reflections and losses, ensuring efficient signal transmission and reception.
High-frequency components generate significant heat. RF PCBs incorporate thermal management solutions, such as the use of materials with high thermal conductivity, to dissipate heat efficiently. This ensures stable performance and longevity of the components.
RF PCBs are built to withstand the stringent demands of high-frequency applications, providing reliable performance in challenging environments such as aerospace, military, and telecommunications. They adhere to standards like IPC-6013 and MIL-PRF-31032 for durability and reliability.
RF PCBs are optimized for high-frequency applications, supporting data rates up to 20 Gbps, which are crucial for modern high-speed digital communications and advanced radar systems.
RF PCBs are essential for applications that require high-speed and high-frequency operation, such as advanced communication systems, medical devices, and defense technologies. Their specialized design ensures they meet the rigorous requirements of these applications.
RF PCB Applications
RF PCBs are essential in various industries due to their ability to handle high-frequency signals with minimal loss. Here are some key applications:
- Smartphones and Tablets: RF PCBs are used for RF communication components such as antennas, RF front-end modules, Bluetooth and Wi-Fi circuits due to their compact design and high-frequency capabilities.
- Smart TVs and Wireless Speakers: Essential for processing and transmitting high-frequency signals required for wireless connectivity and streaming.
- Gaming Consoles: Utilized for wireless communication modules and high-speed data transfer components.
- Wi-Fi Routers: Utilized for handling high-speed data transfer and maintaining signal integrity in wireless networks.
- Automotive Radar: Used in advanced driver assistance systems (ADAS) for collision detection, lane departure warning, and adaptive cruise control.
- Weather Monitoring: Essential for processing and transmitting high-frequency signals in weather radar systems.
- Air Traffic Control: Utilized for reliable and precise signal transmission in radar systems monitoring aircraft movements.
- Transponders and Antennas: Critical for long-distance signal transmission in satellite communication systems, ensuring minimal signal loss and high reliability.
- Onboard Communication Systems: Used in satellites for processing and transmitting high-frequency signals.
- MRI Machines: RF PCBs are utilized in the RF coils and transmitters, which are crucial for generating and detecting the magnetic fields and radio waves used in imaging.
- CT Scanners: Used in the signal processing and communication modules that handle the high-frequency data transmission required for precise imaging.
- Wireless Medical Monitors: Essential for transmitting patient data in real-time, providing accurate and reliable monitoring.
- Navigation Systems: Used in aircraft and spacecraft for reliable signal transmission in navigation and control systems.
- Electronic Warfare Equipment: Critical for high-frequency signal processing in military applications, ensuring robust and reliable performance.
- Keyless Entry: Used in vehicles for reliable and secure wireless communication between the key fob and the vehicle.
- Tire Pressure Monitoring Systems (TPMS): Essential for monitoring tire pressure and transmitting data to the vehicle’s onboard system.
- Infotainment Systems: Utilized for processing and transmitting audio and video signals, providing navigation, internet connectivity, hands-free communication, and integration with smartphones in vehicle entertainment systems.
FAQ
RF boards are specialized PCBs designed to handle high-frequency signals used in various wireless communication applications. Here are the key functions of an RF board:
Signal Transmission and Reception: RF boards enable the transmission and reception of RF signals across various frequencies. This capability is essential for wireless communication systems, allowing devices to send and receive data wirelessly.
Maintaining Signal Integrity: Ensuring proper impedance matching in RF circuits is crucial to maximize power transfer and minimize signal reflection. RF boards are designed with controlled impedance to maintain signal integrity and performance.
Noise and Interference Reduction: RF boards incorporate filters to selectively allow specific frequencies to pass while blocking others. This helps in reducing noise and interference, thus improving the clarity and quality of the transmitted or received signal.
Signal Amplification: RF boards may include amplifiers to boost the strength of weak signals. This is particularly important for applications where signals need to travel long distances or through various obstacles, ensuring that signals remain strong and clear.
Preventing Cross-Talk and Interference: Effective isolation techniques are used in RF boards to prevent different sections from interfering with each other. This design approach helps maintain high signal quality by avoiding cross-talk and signal degradation.
RF PCBs and normal PCBs differ significantly due to the unique requirements and applications of RF circuits. Here’s a detailed comparison:
1. Frequency Range
- RF PCB: Designed to operate at high frequencies, typically in the range of MHz to GHz. These are used in applications such as wireless communication, radar, and satellite systems. High-frequency operation demands specialized design and materials to maintain signal integrity and performance.
- Normal PCB: Operates at lower frequencies, usually below 1 GHz. They are found in general electronic devices like audio systems, household appliances, and automotive electronics. Standard materials and design practices suffice for these applications
2. Material
- RF PCB: Uses specialized materials with low dielectric loss and stable dielectric constant, such as PTFE (Teflon), Rogers materials, or other high-frequency laminates. These materials are crucial for maintaining signal integrity at high frequencies.
- Normal PCB: Typically made from FR-4 (Flame Retardant 4) material, which is suitable for most electronic applications but has higher dielectric loss and less stability at high frequencies .
3. Design Considerations
- RF PCB: Requires meticulous design to minimize signal loss, impedance mismatches, and electromagnetic interference (EMI). The layout must account for controlled impedance, precise trace widths, and spacing. Techniques such as microstrip and stripline are often used.
- Normal PCB: Design focuses more on general electrical and mechanical connections, without the stringent requirements for impedance control and EMI management. Standard design practices are typically sufficient.
4. Signal Integrity
- RF PCB: Signal integrity is a critical concern due to the high frequencies involved. Any impedance mismatch, crosstalk, or signal loss can significantly affect performance. Special care is taken in the design of transmission lines, grounding, and shielding.
- Normal PCB: While signal integrity is still important, the lower frequencies and less complex signals reduce the impact of impedance mismatches and crosstalk .
5. Manufacturing Complexity
- RF PCB: Manufacturing RF PCBs is more complex and requires precision fabrication techniques to ensure the tight tolerances needed for high-frequency operation. This includes careful control of trace dimensions, layer stack-up, and via placement.
- Normal PCB: Manufacturing is relatively straightforward and less costly, with standard fabrication techniques sufficient for most applications.
6. Applications
- RF PCB: Used in applications requiring high-frequency signal transmission, such as mobile phones, Wi-Fi devices, GPS systems, and military radar. These applications demand high performance and reliability at high frequencies.
- Normal PCB: Found in a wide range of applications, from consumer electronics and automotive systems to industrial equipment and medical devices. They are versatile and cost-effective for general electronic applications .
7. Cost
- RF PCB: Generally more expensive due to the specialized materials, stringent design requirements, and precise manufacturing processes.
- Normal PCB: More cost-effective, using widely available materials and standard manufacturing techniques .
Impedance matching in RF (Radio Frequency) PCBs is crucial for ensuring signal integrity and minimizing reflections that can cause signal loss and distortion. The main roles of impedance matching in RF PCBs include:
Optimizing Signal Transfer: Proper impedance matching ensures that the maximum amount of signal power is transferred from the source to the load. This is achieved by making the impedance of the transmission line (PCB trace) equal to the impedance of the load (such as an antenna or another circuit).
Minimizing Signal Reflections: When the impedances of the transmission line and the load do not match, part of the signal is reflected back towards the source. These reflections can interfere with the incoming signals, causing noise, signal loss, and potential damage to components. Impedance matching helps to minimize these reflections.
Maintaining Signal Integrity: At high frequencies, any impedance mismatches can significantly degrade signal quality. Proper impedance matching preserves the integrity of the signal, ensuring that it maintains its intended shape and amplitude. This is crucial for maintaining the performance and reliability of RF circuits.
Reducing Electromagnetic Interference (EMI): Impedance mismatches can lead to radiated emissions, which contribute to electromagnetic interference. By ensuring impedance matching, the PCB design can help minimize these unwanted emissions, improving overall performance and compliance with regulatory standards.
Enhancing Performance of RF Components: Many RF components, such as amplifiers, filters, and mixers, are designed to work at specific impedance levels (commonly 50 ohms). Matching the PCB trace impedance to these components’ impedance ensures they operate efficiently and effectively. This is particularly important in high-frequency applications where even minor mismatches can lead to significant performance degradation.
1. Frequency Range and Application:
- RF PCBs: Typically operate at frequencies from 3 kHz to 300 GHz. They are used in applications such as wireless communication, Bluetooth, Wi-Fi, and other RF communication systems.
- Microwave PCBs: Generally handle higher frequencies, starting from 300 MHz to 300 GHz. They are used in more specialized applications, such as radar systems, satellite communication, and microwave backhaul links.
2. Material Requirements:
- RF PCBs: Can often use standard PCB materials like FR4, but for higher performance, materials with better high-frequency characteristics like Rogers or Taconic laminates are preferred.
- Microwave PCBs: Require materials with very low dielectric loss and stable dielectric constants, such as PTFE (Teflon) or other advanced materials, to handle higher frequencies efficiently.
3. Design and Fabrication Complexity:
- RF PCBs: Usually simpler in design, with fewer layers and less stringent requirements on precision and signal integrity. The designs focus on minimizing losses and ensuring impedance matching.
- Microwave PCBs: More complex, often with multiple layers and intricate designs to ensure proper signal propagation and minimal loss. The fabrication process needs to account for high precision in trace width and spacing, as well as control over the dielectric properties of materials.
4. Thermal Management:
- RF PCBs: Typically generate less heat, so standard thermal management practices suffice. However, efficient heat dissipation becomes crucial when handling high power RF signals.
- Microwave PCBs: Generate significant heat, especially in high-power applications. Advanced thermal management techniques, such as using metal cores or heat sinks, are often required to maintain performance and reliability.
5. Signal Integrity and Impedance Control:
- RF PCBs: Focus on maintaining signal integrity by controlling impedance and minimizing losses through careful design and material selection. Techniques such as using microstrip or stripline configurations are common.
- Microwave PCBs: Require even tighter control of impedance and signal integrity. This involves precise manufacturing processes to ensure that trace dimensions and material properties are within exact tolerances to prevent signal degradation.
The cost of manufacturing RF PCBs is influenced by several factors, each contributing to the overall expense. Key cost drivers include:
Layer Count:
- The number of layers in an RF PCB directly affects its cost. More layers mean more dielectric material, imaging, etching, and plating processes, all of which add to the expense.
Base Laminate Materials:
- The choice of base laminate materials is critical. High-frequency applications often require specialized materials like Rogers or Taconic laminates, which are more expensive than standard FR4. The dielectric constant (Dk) and dissipation factor (Df) are significant considerations, as they impact the performance and cost of the PCB.
Copper Weight:
- Higher copper weights (exceeding 1 ounce) increase costs due to the additional material and the complexity of the etching process. Thicker copper also necessitates more precise control during manufacturing.
Drilling Complexity:
- The density and variety of drilled holes affect the cost. Higher hole density requires more drilling time and frequent drill bit replacements. Additionally, smaller holes and via structures, including laser drilling, add to the expense.
Controlled Impedance:
- Specifying controlled impedance requires precise manufacturing processes and testing, which increase costs. Controlled impedance is often essential for RF PCBs to ensure signal integrity, especially at high frequencies.
Surface Finishes:
- The type of surface finish can impact the cost significantly. Options like immersion gold, silver, or tin, and HASL (Hot Air Solder Leveling) each have different cost implications based on material and process requirements.
Thermal Management:
- RF PCBs often require advanced thermal management solutions, such as metal-backed laminates or embedded heat sinks. These methods ensure efficient heat dissipation but add to the overall manufacturing cost.
Mechanical Processing:
- Complex mechanical features like cavity constructions, edge plating, and specific milling requirements increase costs due to the additional processing steps involved.
Panel Utilization and Delivery Array:
- Efficient panel utilization can reduce costs. Early coordination with the manufacturer to optimize the design and delivery array can bring significant savings by maximizing material use and minimizing waste.
Quality and Testing:
- Extensive testing for electrical integrity, impedance, and reliability, including the use of flying probes or bed-of-nails test fixtures, adds to the manufacturing cost. Ensuring high-quality standards is essential for RF PCBs, given their critical applications.
The performance of RF (Radio Frequency) PCBs is influenced by various factors that impact signal integrity, thermal management, and overall functionality. Key factors include:
Material Selection:
- High-frequency applications require materials with low dielectric loss and stable dielectric properties over a range of frequencies and temperatures. Common materials include Rogers, Taconic, and PTFE-based laminates, which provide better performance than standard FR4.
Conductor Surface Roughness:
- Surface roughness of the copper traces can increase resistance and signal loss, especially at higher frequencies. Smooth copper foils (e.g., rolled annealed copper) are preferred to reduce these losses.
Thermal Management:
- Efficient heat dissipation is essential to prevent performance degradation and ensure reliability. Techniques include using thermal vias, metal-backed substrates, and heat sinks to manage the heat generated by high-frequency signals.
Impedance Control:
- Maintaining consistent impedance throughout the PCB is critical for minimizing signal reflections and ensuring signal integrity. This requires precise control over trace width, spacing, and the dielectric properties of the materials used.
Via Design and Placement:
- Vias introduce inductance and capacitance, which can affect high-frequency performance. Minimizing the use of vias, using back-drilled or blind vias, and ensuring proper via placement are strategies to mitigate these effects.
Trace Width and Spacing:
- The dimensions and spacing of traces must be carefully controlled to avoid crosstalk and maintain consistent impedance. Microstrip and stripline configurations are commonly used in RF PCB design to achieve these goals.
Environmental Stability:
- The PCB materials must maintain their electrical properties across the operating temperature range and environmental conditions. This includes stability in humidity and resistance to thermal expansion and contraction.
Via design plays a crucial role in the performance and reliability of RF (Radio Frequency) PCBs. Here are the key aspects of via design and their significance:
Ensuring Signal Integrity
- Vias introduce inductance and capacitance, which can affect the integrity of high-frequency signals. Proper via design helps minimize these parasitic effects, ensuring that signals maintain their integrity as they transition between layers. For instance, using back-drilled vias or controlled depth vias can reduce the inductive effects of unused via stubs. This approach helps maintain the quality of the signal without distortion or loss.
Enhancing Thermal Management
- Vias are often used for thermal management, providing paths for heat to dissipate from high-power components to the ground or other heat sinks. Properly placed thermal vias under components like power amplifiers and RFICs ensure efficient heat dissipation, which is crucial for maintaining performance and reliability. Effective thermal management helps prevent overheating and maintains the operational stability of the PCB.
Improving Mechanical Stability
- Vias enhance the mechanical strength of the PCB by providing additional interconnections between layers. This is especially important in multilayer RF PCBs, where the mechanical stability of the board can affect overall performance. The mechanical stability provided by vias ensures the PCB can withstand physical stresses and maintain its structural integrity during operation.
Enhancing Isolation and Shielding
- Vias are used to create via fences or via stitching, which help isolate and shield sensitive RF traces from noise and interference. By placing vias around critical signal traces, designers can create effective barriers that enhance signal integrity and reduce crosstalk. This shielding effect is vital in maintaining the performance of RF circuits in environments with high electromagnetic interference.
Facilitating Effective Layer Transitions
- When signals transition between layers, the return path for the RF current must be carefully managed to prevent discontinuities that can lead to EMI (Electromagnetic Interference) and crosstalk. Using vias correctly ensures that the return path is maintained, reducing the potential for these issues. Properly designed vias help manage the transition smoothly, maintaining signal integrity across layers.